To test oil blend stability over time, you'll need to monitor samples in controlled conditions using temperature-regulated incubators and proper storage containers. Track changes in viscosity, color, and odor while conducting regular pH tests and oxidation assessments. Document your observations of physical properties and use UV exposure testing to evaluate degradation rates. Consider accelerated aging techniques with OXITEST equipment for faster results. Proper documentation and systematic testing will reveal your blend's true stability profile.
Equipment and Materials Required for Stability Testing
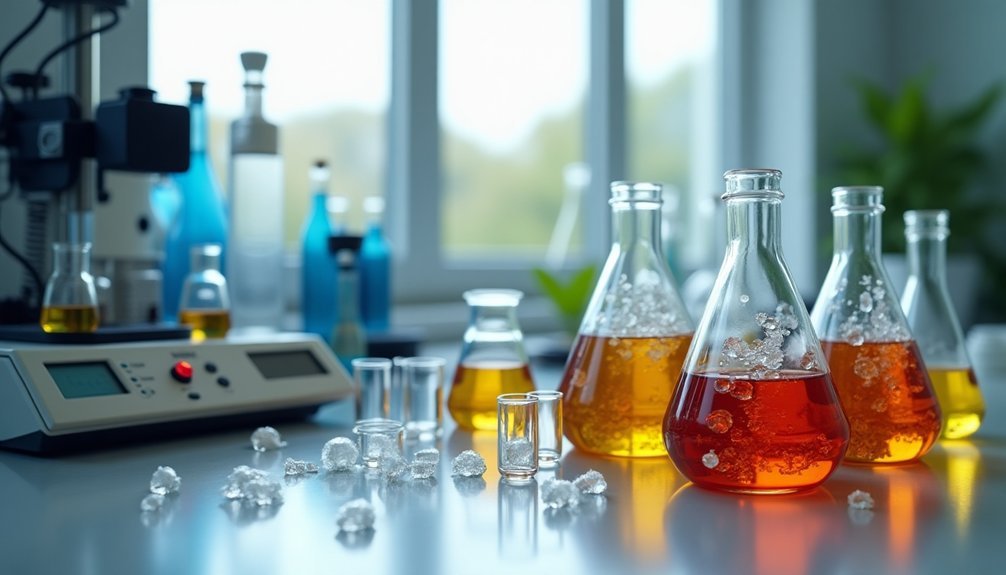
When conducting stability tests on oil blends, you'll need several essential pieces of equipment and materials to guarantee accurate results.
Start with a temperature-controlled incubator and shaking apparatus to monitor your samples under controlled conditions. You'll also require a viscometer to track viscosity changes throughout the stability testing period.
For proper sample storage, use glass containers or amber bottles to protect your oil blends from light exposure and prevent photo-oxidation.
Include pH strips or meters to monitor preservative effectiveness, and gather necessary analytical reagents for oxidation stability analysis.
If you're conducting advanced testing, you'll want access to analytical equipment like gas chromatography or mass spectrometry to detect volatile compounds.
Don't forget to stock up on your sample oils, preservatives, and stabilizers before beginning your tests.
Initial Sample Preparation Guidelines
Before starting any oil blend stability test, proper sample preparation forms the foundation for reliable results. You'll need to collect at least 100 grams of each oil blend you're testing to guarantee you have enough material for thorough analysis.
Work in a clean, dry space and use glass or high-quality plastic containers to prevent unwanted chemical interactions. Label each container with essential details including blend composition, preparation date, and any specific characteristics.
To maintain stability during testing, store your samples in a controlled environment away from sunlight and at a consistent temperature.
During sample preparation, document key observations about color, viscosity, and odor. These initial measurements will serve as your baseline for tracking changes and evaluating the stability of your oil blends over time.
Temperature Control Parameters
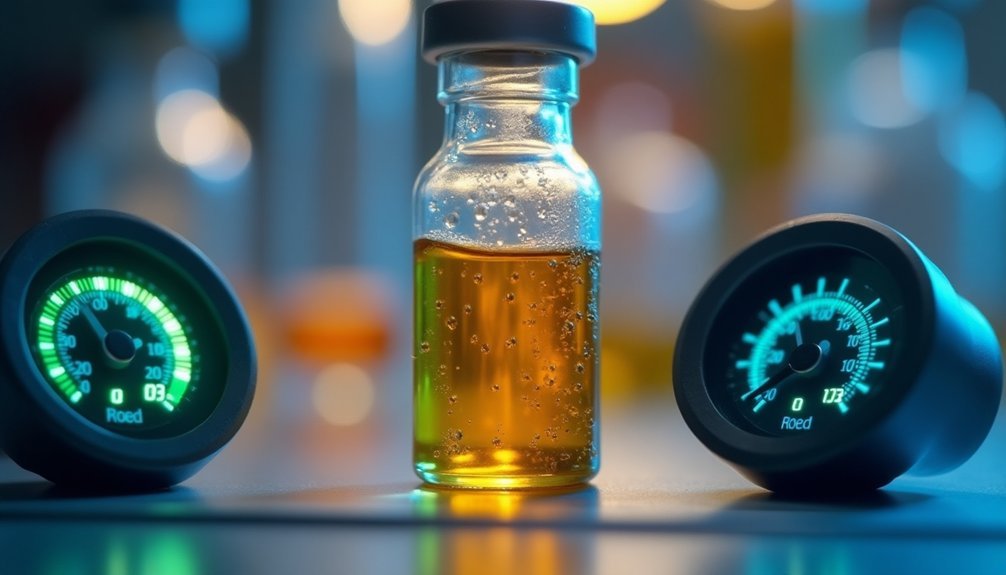
Since temperature directly impacts oil degradation rates, establishing precise temperature control parameters is vital for reliable stability testing.
You'll need to maintain temperatures between 25°C and 60°C, depending on your testing objectives. Higher temperatures will accelerate oxidation, helping you predict long-term stability and compatibility outcomes more quickly.
To guarantee accurate results, you'll want to use calibrated incubators or temperature-controlled environments.
It's important to regularly verify your monitoring equipment's accuracy, as even minor temperature variations can skew your findings.
Make sure you're documenting all temperature conditions throughout your testing period. This systematic approach helps you track how different oil blends respond to specific thermal conditions and allows you to replicate your tests effectively when needed.
Light Exposure Testing Protocols
When testing oil blend stability, you'll need to place your samples under controlled UV light exposure using standardized fluorescent or ultraviolet lamps that simulate long-term environmental conditions.
You should set up a weekly monitoring schedule to track progressive color changes, which serve as visual indicators of oxidation and degradation.
Your observations of color shifts from clear to yellow, brown, or darker hues will help determine the effectiveness of your formulation and any needed adjustments to improve stability.
UV Light Exposure Methods
Testing oil blend stability through UV light exposure provides a reliable method to simulate natural sunlight degradation in an accelerated timeframe.
You'll need to place your oil samples in UV-transparent containers and expose them to controlled UV light exposure testing to evaluate their stability reserve and compatibility over time.
Monitor your samples regularly throughout the exposure period, which can last from several hours to multiple days. You should check for key indicators of degradation, including changes in color, viscosity, and odor.
Pay attention to the induction period (IP) – a shorter IP suggests your oil blend has lower stability and oxidizes more quickly.
For thorough results, combine this method with other stability tests like OXITEST to get a complete picture of your oil blend's performance under various conditions.
Monitoring Color Changes Weekly
Regular color monitoring serves as an essential component of UV light exposure testing, building upon the broader stability assessment methods.
You'll need to track your oil blend's color changes weekly using a spectrophotometer for consistent, objective measurements.
Start by documenting your baseline color values before exposure testing. Place your samples under controlled UV light conditions or direct sunlight to simulate real-world scenarios.
Each week, measure and record any shifts from the original hue. Pay close attention if your oil shifts from light yellow to darker amber, as this signals potential degradation.
Keep detailed records of all measurements to establish clear trends in your oil's stability over time.
If you notice significant color changes, it's time to conduct additional quality tests to evaluate the blend's overall condition.
Oxidation Assessment Methods
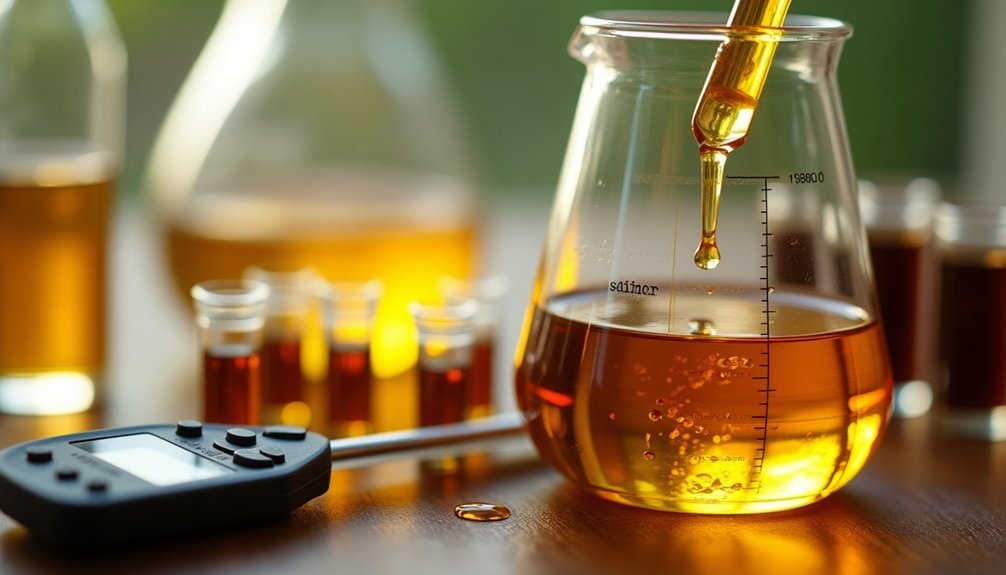
Three primary methods stand out for evaluating oil blend oxidation stability.
First, you'll want to use the OXITEST method, which speeds up oxidation testing by combining high temperatures with oxygen pressure. This gives you faster results compared to traditional testing that could take months.
OXITEST revolutionizes oxidation testing by using heat and oxygen pressure, delivering results in a fraction of traditional testing time.
Next, you'll need to perform visual inspections following ASTM D 4176 guidelines. Look for signs of haze, darkening, or floating particles that might indicate quality issues.
Finally, utilize the OXISoft software to analyze your OXITEST results, particularly the Induction Period (IP) measurements. Longer IP values show better stability.
These oxidation assessment methods work together to help you evaluate Oil Stability and monitor antioxidant effectiveness.
You'll get thorough insights into how your oil blends perform under various conditions.
Chemical Compatibility Monitoring
You'll need to conduct material reactivity tests to understand how different oil components interact and identify potential incompatibilities before they cause problems.
Regular blend separation analysis using light back-scattering techniques can help you track the stability reserve of your oil mixtures and predict flocculation issues.
To complete your compatibility assessment, measure oxidation rates under various environmental conditions, which will reveal how temperature and other factors affect your blend's long-term stability.
Material Reactivity Tests
Testing an oil blend's chemical compatibility with various materials is essential for ensuring long-term stability and performance.
You'll need to conduct material reactivity tests by exposing your oil blends to different metals and plastics, carefully observing any interactions that could affect the oil's properties.
To get reliable results, use standardized testing methods like ASTM D 4052 and ASTM D 4176. These protocols help you monitor potential issues such as oxidation and polymerization that might compromise your oil blend's quality.
Keep detailed records of your test outcomes, as this documentation will guide your decisions about formulation adjustments and packaging materials.
Regular chemical compatibility monitoring enables you to identify and address stability concerns before they become serious problems, ensuring your oil blends maintain their intended characteristics throughout their lifecycle.
Blend Separation Analysis
When monitoring oil blend stability, regular separation analysis serves as a critical indicator of chemical compatibility. You'll need to conduct systematic sampling and visual inspections to identify changes like cloudiness or layer formation that signal potential instability in your mixture.
To gather quantitative data, you can employ light back-scattering and spectrophotometry techniques. These methods help you detect incompatibility early, allowing for timely adjustments. You should also measure asphaltene concentration and monitor their aggregation tendency, as these factors directly impact the blend's stability reserve.
Throughout your testing period, track changes in viscosity and pH levels. These measurements provide valuable insights into chemical compatibility shifts.
Oxidation Rate Measurement
Monitoring oxidation rates provides essential data about your oil blend's long-term stability and resistance to degradation.
You'll want to use the OXITEST method to accelerate the oxidation process, which measures your blend's Induction Period (IP) under controlled temperature and oxygen pressure conditions. A longer IP indicates better oxidation resistance.
To maintain accurate stability reserve measurements, you'll need to regularly check your oil's oxidation rates through light back-scattering techniques.
Don't forget to add appropriate antioxidants to enhance your blend's stability – they can greatly improve IP values.
You can further protect your oil blend by storing it properly away from light and heat exposure.
This thorough oxidation rate measurement approach helps you predict when your blend might start degrading, allowing for timely intervention.
Physical Property Measurements
Physical property measurements serve as fundamental indicators of an oil blend's stability and performance characteristics.
You'll need to monitor key parameters including viscosity, density, and specific gravity to track changes in your oil's composition over time.
Using ASTM D445 standards, you can measure kinematic viscosity, which will alert you to potential polymerization or degradation.
You'll want to regularly check pH levels, as they directly impact preservative effectiveness and overall stability.
Don't forget to employ optical tests using light back-scattering techniques to detect asphaltenes and particulates that might affect your blend's compatibility.
Keep track of color and odor changes too – they're valuable qualitative indicators of oxidation and rancidity.
These simple observations can help you determine your blend's shelf life and continued usability.
Accelerated Aging Techniques
You'll discover reliable oil blend stability insights through accelerated aging techniques that combine precise temperature controls with high-pressure oxygen exposure in specialized chambers.
Your testing regime should include controlled light exposure assessments using UV lamps or sunlight simulators to evaluate photo-oxidation effects.
These controlled stress methods let you quickly identify potential stability issues that might take months or years to surface under normal storage conditions.
Temperature Control Methods
When testing oil blend stability, accelerated aging techniques provide efficient ways to simulate long-term storage conditions.
You'll need to implement precise temperature control methods to maintain consistent testing environments between 60°C to 80°C using specialized ovens or temperature chambers.
To assess oxidative stability effectively, you'll want to monitor your samples periodically through viscosity checks, color observations, and smell evaluations.
Set specific testing durations, such as 30, 60, or 90 days, to track changes systematically.
For more thorough results, you can employ temperature cycling, alternating between high and low temperatures to replicate real-world storage and transport conditions.
This approach helps you understand how your oil blends perform under varying environmental stresses, ensuring you get reliable data about their long-term stability performance.
Oxygen Exposure Testing
To accelerate the aging process of oil blends, oxygen exposure testing offers a reliable method for evaluating long-term stability in a compressed timeframe.
You'll need to place your oil samples in a controlled environment with elevated temperature and pressure to speed up oxidation.
During the testing process, you should monitor key indicators like the induction period (IP), which tells you how long it takes before significant oxidation begins.
The longer the IP, the more stable your oil blend.
You'll want to track changes in viscosity, color, and rancidity throughout the test to understand your product's degradation pattern.
This testing method helps you assess how effective your antioxidants and stabilizers are at extending shelf life, letting you optimize your formulations before bringing products to market.
Light Degradation Analysis
Light exposure plays a vital role in oil blend stability testing, making controlled degradation analysis an essential part of your development process. By using specific wavelengths to accelerate oxidation, you'll reduce testing time from months to days while gaining valuable insights into your oil blend's stability.
During light degradation analysis, you'll monitor significant changes in:
- Color variations that indicate chemical transformations
- Viscosity shifts that affect product performance
- Formation of oxidation products that impact shelf life
You can use this data to predict real-world stability and optimize your formulations. The process helps you evaluate antioxidants and stabilizers effectively, ensuring your final product maintains its intended properties.
Documentation and Record Keeping
Since successful oil blend testing relies heavily on proper record keeping, implementing a robust documentation system should be your top priority. You'll want to track each blend's formulation, testing results, and stability assessments digitally for easy updates and retrieval.
Documentation Element | Testing Frequency | Key Data Points |
---|---|---|
Formulation Records | Initial Creation | Ingredients, Ratios |
Stability Tests | Monthly | pH, Color, Viscosity |
Shelf Life Data | Ongoing | Best Before Dates |
Set up a monthly testing schedule to monitor your blends' stability and maintain detailed records of any changes you observe. Don't forget to clearly label each product with best before dates, even when they're not required by law. Your documentation should capture all essential observations throughout the product's shelf life, ensuring you can track performance and safety effectively.
Quality Control Checkpoints
Regular quality control checkpoints serve as your frontline defense against potential stability issues in oil blends.
You'll need to monitor pH levels consistently to guarantee your preservatives remain effective and your product stays safe. When conducting stability testing, remember to check for visual changes like separation, color shifts, or sediment formation.
- Don't skip your predetermined testing intervals – they're vital for tracking how your blend's viscosity, appearance, and odor evolve throughout its shelf life.
- Pay close attention to environmental factors like temperature and humidity, as they can greatly impact your oil's stability.
- Stay vigilant with your documentation – every test result matters, especially when you're modifying your formulation.
Remember to retest your blend whenever you make changes to maintain your product's integrity and your customers' confidence.
Corrective Action Strategies
When stability issues arise in your oil blends, implementing swift and targeted corrective actions can prevent further degradation and salvage your product.
Start by reviewing your test results to identify the specific stability problem, whether it's oxidation, viscosity changes, or contamination.
If you've detected early signs of oxidation, immediately add appropriate antioxidants and metal deactivators to slow down the degradation process.
You'll need to adjust your storage conditions if environmental factors are affecting stability – consider temperature-controlled areas away from direct light.
Document every corrective measure you implement and conduct follow-up stability tests to verify their effectiveness.
When your test results show persistent issues, you might need to reformulate your blend or modify your production process to enhance long-term stability and product quality.
Frequently Asked Questions
What Is the Oxidation Stability Test for Oils?
You'll find that OXITEST speeds up oil oxidation under controlled temperature and oxygen pressure to determine stability. It measures the Induction Period, where oxygen consumption indicates how well your oil resists degradation.
How to Test Essential Oil Blends?
You'll need to store your essential oil blends in clear glass containers, check pH regularly, monitor changes in appearance and scent, and document all observations over time. Compare fresh and aged samples periodically.
How to Do a Fuel Compatibility Test?
You'll need to analyze crude oil samples with ASTM D 7112, measure asphaltene content, and apply the K-model. Check viscosity ratios, use light back-scattering techniques, and monitor for visual signs of incompatibility.
How to Measure Oxidative Stability?
You'll need to use the OXITEST method to measure oxidative stability. Place your oil sample under high temperature and oxygen pressure, then monitor the Induction Period to determine how long before oxidation begins.
In Summary
You'll find that regular testing and documentation of your oil blend's stability is essential for maintaining product quality. Follow proper storage conditions, conduct periodic assessments using standardized protocols, and implement corrective measures promptly when needed. By monitoring temperature, light exposure, and oxidation levels consistently, you're ensuring your blend remains stable and meets quality standards throughout its intended shelf life.
Leave a Reply